Bonded and mechanical anchors – how to choose the right fixing?
Choosing the right fixing guarantees safe, secure, and durable installation. You can choose between traditional mechanical anchors and bonded anchors. What are the differences between these types of fixings, how do they work, and what should you pay attention to when choosing? Check it out!
Anchors, as opposed to wall plugs, can carry very high loads. Most often, we use them to fix two parts of a structure together, or to fix structural elements to concrete and other substrates. For example, anchors can be used to install steel, aluminium or timber components (e.g., balustrades) in concrete (mainly in the case of mechanical anchors) or masonry substrate (in the case of bonded anchors).
Anchor types and the main differences between them
There are two main types of anchors:
- Mechanical anchors, which use the force of expansion in the base material,
- Bonded anchors, which use adhesion force, creating a surface bond.
Mechanical fixing is the traditional type of anchoring using steel fixings. Bonded anchors, on the other hand, require appropriate application and can only be loaded after setting.
Zawartość artykułu
- Anchor types and the main differences between them
- Mechanical anchors – properties and applications
- [►video] Shortcuts! Mechanical anchoring in concrete
- Steel anchor types and applications
- What are bonded anchors and how do they work?
- [► video] Shortcuts! Browse and watch videos about bonded anchors:
- Bonded anchor types and applications
- Bonded or mechanical – choosing the right anchor
- Pros and cons of metal and bonded anchors
- Mechanical anchors – advantages
- Disadvantages of steel anchors
- Bonded anchors – advantages
- Disadvantages of bonded anchors
- Bonded vs mechanical anchors: applications
Important note:
There are cases in which mechanical and bonded anchors can be used interchangeably. However, you need to take into account specific guidelines and factors in order to choose the best fixing for the job, i.e. the safest and most durable one. User preferences and installation convenience are secondary considerations.
Mechanical anchors – properties and applications
These anchors fix components to the substrate by physical force. The mechanism of action is similar to that of the wall plug. An exception is provided by concrete screws, which undercut the substrate and, thanks to their thread grooves, become embedded along the entire length of the hole.
Did you know that…
Mechanical anchors are also referred to as concrete anchors, steel anchors, and metal anchors. With a few exceptions, they are designed exclusively for concrete substrates.
Concrete anchors are the type used most frequently for heavy-duty fixing, and they are suitable for virtually any construction site. They are appreciated for the quick installation and simple application, at the same time ensuring high load capacity.
All mechanical anchors (or at least their main components) are made of steel, which is why they are called metal anchors or steel anchors, for the sake of simplicity. However, you need to remember that some of them also contain plastic elements.
Despite their undisputable advantages, metal anchors have some drawbacks. These are mostly related to the installation method and to the physical forces involved. The high stresses to which the anchor is constantly exposed and its expansion against the substrate structure can cause the base material to crack, spall, and become detached.

[►video] Shortcuts! Mechanical anchoring in concrete
Steel anchor types and applications
There are several types of steel anchors for concrete. To choose properly between bonded and chemical anchors, it is worth getting to know them better.
- Screw-in anchors (also known as concrete screws) represent a special type of metal anchor that does not expand the base material, and therefore does not damage it. These fixings are quick and convenient to install, and can be removed and reinstalled in the same hole, which makes them good for temporary installation. They also make it possible to securely fix elements with medium to heavy loads.
- Throughbolts are designed for through installation, which is a relatively quick and uncomplicated method. To drill the hole, you should use a drill bit of the same diameter as the anchor itself. The different anchoring depths allow throughbolts to fix elements with different thicknesses.
- Sleeve anchors are quite versatile: they are designed for low to medium loads. These anchors are used mainly to install various systems in concrete. Mechanical sleeve anchors also include internally brass and steel wedge anchors with internal thread. They are also referred to as hammer-in sleeve anchors because of the installation technique using a setting tool or a hammer, as well as a bolt or threaded rod.
- Shield anchors are expansion anchors that contain all the components needed for installation – a rod or bolt, a nut, a flange, or a hook, for example. They are highly versatile mechanical anchors, designed for substantial loads and all types of substrates.
- Metal frame anchors are special metal anchors designed for easy and quick installation of door and window frames, with a special design preventing deformation of the frame during application.
What are bonded anchors and how do they work?
Bonded anchors, also known as chemical anchors, are fixings based on a bond created when the resin mixes with the hardener. The operating principle is based on the phenomenon of adhesion, i.e. superficial bonding of two substances. These properties of bonded anchors make them widely applicable, especially in building renovation.
They are particularly robust and versatile fixings. Their advantage, as opposed to metal anchors, is that they are non-invasive: they do not generate stresses in the substrate and thus do not contribute to its destruction or weaken the structure.
Learn how to prepare a hole for chemical anchoring.
Did you know that…
Chemical anchors have been known since the 1960s. They were used in the first time in 1972 during the construction of the stadium in Munich where the summer Olympic Games were held. No other type of fixing proved to be effective in the case of similarly short distances between anchors and very near edges. Metal anchors were not suitable for this task due to their expansion properties.
Bonded anchors offer extensive possibilities of application: they can be used in any substrate and in a variety of conditions, even in wet environments. They do not succumb to corrosion, they are excellent for deep anchoring and, above all, they are capable of withstanding even the highest forces. Their load capacity is excellent.
It is worth bearing in mind that the installation of bonded anchors needs to be well-though-out and carefully planned, due to the setting time of the chemicals. The application of bonded anchors also requires precision and compliance with the instructions provided, as well as the use of suitable dispensers. Chemical fixings cannot be dismantled and are therefore not suitable for temporary structures or any installation where changes will subsequently need to be made.
Important note:
The advantage of bonded anchors is that they are perfect for permanent fixing in materials with hollow spaces, such as vertically perforated brick and hollow masonry units. However, you need to remember that removal will be more complicated in this case (it will involve cutting out or drilling out the entire anchor), leading to the creation of large cavities that will have to be filled.
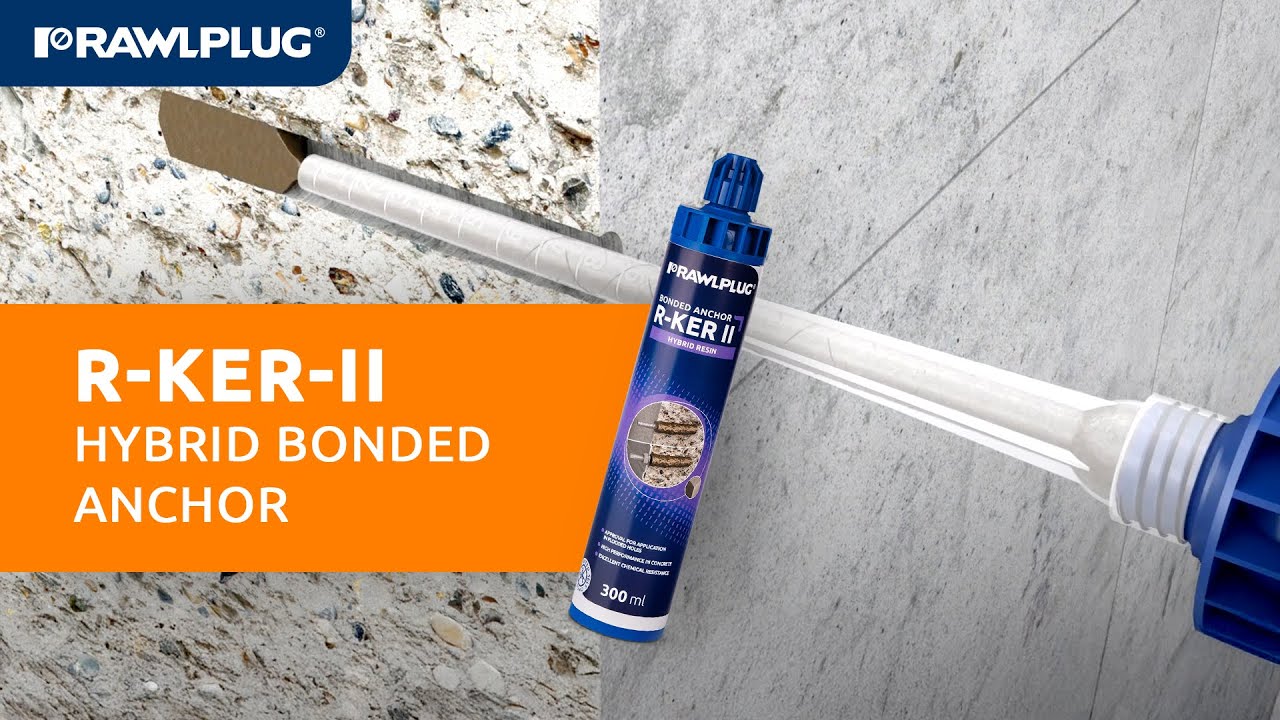
[► video] Shortcuts! Browse and watch videos about bonded anchors:
Bonded anchor types and applications
Different types of anchors are available depending on the type of resin compound they contain:
- Vinylester resin for concrete, delivered in capsules. These bonded anchors can be used for very high loads. They come in two versions: hammer-in and screw-in. Installation of bonded anchors in capsules is very convenient, as they already contain the right amount of resin and hardener, and no special accessories are required. They can be used for both dry and wet concrete.
- Polyester bonded anchors designed for low to medium loads, very versatile, durable and available in different versions depending on the drying time, so that they can be used in different thermal conditions. Polyester bonded anchors are intended mainly for solid substrates, but in combination with mesh sleeves, they can also be used in hollow materials.
- Epoxy resin – these anchors carry the highest loads, but do not perform well in winter conditions due to slow setting. However, the long setting time also has its advantages, as it makes it easier to install steel components at high temperatures (you have more time to install the rods). These anchors are also perfect for deep rebar anchoring with depths of up to 2.5 m.
- Hybrid bonded anchors for concrete, combining the properties of epoxy resin and polyester anchors, and thus more versatile. They can withstand very high loads and come in different versions for installation in different weather conditions. They are suitable for deep anchoring (up to 1.5 m).
<strong>Important note:</strong>
Bonded anchors vary in terms of setting time, due to their composition, but also due to weather conditions (temperature and humidity of the air or dampness of the substrate). Remember to choose your product properly. Our range includes, for example, hybrid bonded anchors in summer or winter versions.
Learn how long does it take a bonded anchor to set.
The following types of bonded anchors are distinguished depending on the primary packaging:
- anchors in plastic cartridges, for which a cartridge dispenser gun is required;
- anchors in soft-skin capsules (foil packs), for which another special dispenser gun is used;
- anchors in glass capsules that do not require dispenser guns.
Need accessories for bonded anchors?
Meet Rawlplug’s bonded anchor dispenser guns.
Bonded or mechanical – choosing the right anchor
Before you decide which anchor to choose, you should consider a number of aspects. Only then will you be able to select the right type of anchor for concrete or other substrates.
Here are the factors to take into account when choosing between a steel anchor and a bonded anchor:
- Substrate type – it is not only the type of base material that is important, but also its condition, grade, and structure. How compact the substrate is has an enormous impact on the durability of the fixing and on whether it will lead to damage of the material, putting the entire structure and the safety of its use at risk.
- Environmental conditions – important both during the installation process (only in the case of bonded anchors) and for post-installation durability. Wherever an anchor may be exposed to moisture and low temperatures, you should choose metal anchors with additional anti-corrosion coatings, or bonded anchors, which mostly perform best in all weather conditions. However, you need to make sure that you choose the right bonded anchor in terms of the setting time, which varies depending on the temperature.
- Installation distances – if the elements to be fixed are close to each other or close to edges, using a mechanical anchor can be risky or even impossible. For such jobs, less invasive bonded anchors tend to be better, as their operating principle is not expansion, but adhesion.
- Weight and type of the element being fixed – each anchor for concrete and other substrates is provided with an indication of its strength (load capacity). Always choose your anchor appropriately so that it can withstand the load without any problems. Manufacturers are also able to predict how many years a particular fixing can last. Bonded (chemical) anchors are most resistant to very high loads, as they can carry up to 200 kg in hollow substrates, and 800 kg in solid substrates. Mechanical anchors are recommended for lower loads.
- Load type and direction – in addition to weight, it is also important how the element being fixed will be used, as this will physically affect the entire structure. Loads can be static (in these cases, steel anchors work well) or dynamic (in these cases, bonded anchors may be better, due to their non-invasive operating mechanism). The load direction also matters: it can be tension (when the load is parallel to the anchor and we are dealing with a pull-out force) or shearing (when the load is fixed at an angle).
- Fixing parameters – the possible anchoring depth and the kind of holes that can be drilled are also important aspects. Consequently, the choice of anchor should match the installation guidelines as closely as possible.
Important note:
Make sure you reach the minimum embedment depth that guarantees that the anchor can carry the load safely.
Pros and cons of metal and bonded anchors
Finally, it is worth listing all the advantages of each solution, which will help us answer the question of which anchor to choose.
Mechanical anchors – advantages
- Possibility of immediate loading.
- Installation regardless of thermal conditions.
- Excellent performance in solid substrates.
- Good performance in through installation, speeding up fixing.
- Steel concrete anchors (screws) are perfect for temporary installation, as they can be completely removed from the substrate.
- Generally cheaper than bonded anchors.
- Less demanding installation.
Disadvantages of steel anchors
- Not suitable for hollow and masonry substrates (apart from a few exceptions and non-professional applications).
- They expand the substrate, so they cannot be used close to other anchors or near edges.
- They can corrode, especially if they are chosen improperly with regard to the conditions and material they may come into contact with.
- They cannot be installed in damp substrates or under any chemical conditions.
Bonded anchors – advantages
- Highest load capacities and possibility of deep anchoring.
- An alternative to mechanical anchors when dealing with non-concrete and damaged substrates.
- Resistance to dynamic loads (vibrations).
- A small distance between anchors can be maintained and fixing can be performed close to edges.
- Suitable for all types of substrates, also damaged and with hollow spaces, as well as damp, wet, and flooded.
Disadvantages of bonded anchors
- Installation of bonded anchors is more complicated. They cannot be loaded immediately after application, as they have a specific setting time you must strictly adhere to, which depends on the thermal conditions.
- They require special accessories for application: a dispenser gun, a brush, or a pump.
- The temperature of the chemicals, i.e. the operating temperature, is also important. Under 5°C, a cartridge cannot be used. When working in low temperatures, you need to be particularly careful about this, and also pay attention to the conditions in which the bonded anchors are stored. It is essential that you adhere strictly to the rules specified on the label.
- These anchors generally cannot be dismantled, which makes them unsuitable for temporary installation.
Bonded vs mechanical anchors: applications
What are the applications of bonded anchors versus mechanical anchors? A good way to quickly compare them is by looking at where they are used most frequently. This will help you choose the right anchor already at the start.
Mechanical anchor applications:
- fixing of various structural components (pole bases, beam supports, handrails);
- installation of various shelving units;
- construction of industrial doors;
- installation of ventilated facades;
- lightweight suspended ceilings.
Bonded anchor applications:
- renovation of civil engineering structures (bridges, residential, office and production buildings) as well as various repair and renovation work, also in places where mechanical anchors were previously installed;
- alterations, extensions, superstructures;
- reinforcement;
- construction of roads and other infrastructure.
In summary, when choosing your anchor, you need to take into account many factors and consider all sorts of aspects. This is not a difficult task provided that you establish your basic needs, and when in doubt, it is always worth looking at the specifications and detailed descriptions of the products as well as and the manufacturers’ recommendations.
In a nutshell, go for a mechanical anchor if you want to perform installation quickly in dry, undamaged concrete, and choose a bonded anchor if you need to fix a very heavy component in an unreliable substrate.
Want to know more?
Check out this Rawlplug YouTube playlist, where you can find a lot of information about different kind of anchors and fixings together with tutorials and instructions.